What is a BLDC Motor?
A BLDC Motor that is brushless has no brushes, as the name suggests. The rotor and the stator are the two distinct parts that make up a brushless motor. BLDC Motor has revolutionized the world of electric motors, offering numerous advantages over their brushed motor. In this comprehensive guide, we will explore the principle of operation of brushless dc motors, highlighting their key features, benefits, and applications. Whether you are an enthusiast looking to build your own drone or someone interested in understanding the inner workings of these motors.

What is BLDC Motor Thrust?
Thrust is a reaction force described quantitatively by Newton’s third law. When a system expels or accelerates mass in one direction, the accelerated mass will cause a force of equal magnitude but opposite direction to be applied to that system. The force applied on a surface in a direction perpendicular or normal to the surface is also called thrust. A fixed-wing aircraft propulsion system generates forward thrust when air is pushed in the direction opposite to flight. This can be done by different means such as the spinning blades of a propeller, the propelling jet of a jet engine, or by ejecting hot gases from a rocket engine. Reverse thrust can be generated to aid braking after landing by reversing the pitch of variable-pitch propeller blades. Rotary wing aircraft use rotors and thrust vectoring V/STOL aircraft use propellers or engine thrust to support the weight of the aircraft and to provide forward propulsion. BLDC motor thrust, to put it simply, is the maximum upward force your drone can create when it is fully charged.
Refer to Wikipedia: https://en.wikipedia.org/wiki/Thrust
Why does Thrust Matter for FPV Motor?
Oftentimes, thrust is the primary consideration when selecting a bldc motor. It is, after all, the force that gives your drone its lift and enables it to carry out those amazing aerial stunts. Higher thrust leads to faster acceleration, although efficiency and current draw are also important considerations. Selecting motors and propellers combination that requires high current will overtax your batteries and reduce their longevity. Ascertain that your battery’s maximum discharge rate is sufficient for the work if your drone uses a considerable quantity of electricity when it is operating at a high throttle. Therefore thrust is certainly an important aspect to consider when choosing FPV motors.
If you want to learn more about the knowledge of choosing motor, read this guide on How to choose fpv drone motor a detailed guide 2024

Calculating Thrust-to-Weight Ratio For FPV Drone
By adding up the entire weight of your quad components (all-up weight, or AUW) and comparing it to the estimated thrust for your motor, prop, and lipo battery combination, you can calculate the thrust-to-weight ratio of your possible quad construction. You can determine how light or heavy your quad feels in the air by figuring out its thrust-to-weight ratio.
A quad’s total weight can be easily determined by summing the weight of all of its components and payload (such as a GoPro, if you want to fly one) in grams. The wiring and other accessories, such as battery straps, will require an additional 20–25 grams. It seems sense that you can estimate this and change it later if you haven’t chosen any parts yet besides your frame. Use the product information to determine the grams that each of the other parts you’ve picked for your quad, such as the flight controller or video transmitter, weighs.
It’s trickier to calculate thrust without first purchasing the necessary parts and conducting your own experiments. Due to the limited product information available, we can only estimate thrust. Because it’s simple to use and provides a reliable estimate of the amount of thrust to anticipate, this estimation approach is excellent. This technique works with any bldc motor that has thrust table information. As an alternative, you might Google motor thrust testing that have previously been carried out. You must view the motor thrust tables and navigate to the motor’s product details in order to estimate thrust without having to purchase your parts beforehand.
You can see how the quad motors work with a particular prop and battery combination in these tables. Find out how much thrust a certain prop and battery combination can produce in grams at maximum throttle.
Example Thrust-to-Weight Ratio Calculation:With MEPS 2207 for Example
Assume for the moment that the total weight of our 5-inch quad was 1000g. MEPS 2207 thrust chart:
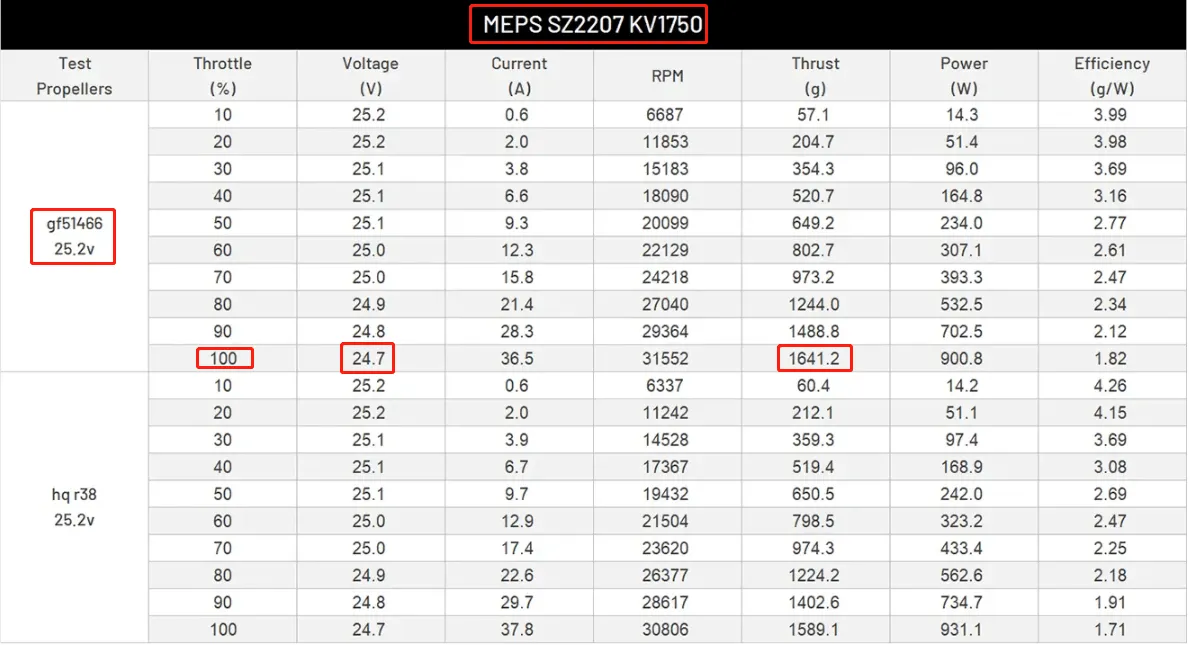
We can determine that MEPS motors 2207 are generally suitable for 5-inch quads by using our motor criteria. In the chart (which is boxed in red), we discovered the maximum thrust is 1641.2g throuh the match of meps motors 2207, propellers and battery (shown by the voltage) . We’ll multiply that by four because we’re making a quadcopter, and the result is 6564.8g of thrust.
So for this match, the thrust-to-weight ratio at maximum thrust is 6564.8 : 1000 ≈ 6.7 : 1
If this is the kind of quad you want, you may decide with your thrust-to-weight data. Generally speaking, you want to aim for a ratio of at least 2:1 so that your quad can stay at half-throttle. This exercise will help you to alter your fpv motors need based on the type of flying you choose to accomplish. To change the feel, you can also change the sections that make up your total weight. The more thrust to weight ratio, your quad will have greater responsiveness.
The thrust-to-weight ratio should be much higher for racing drones than it is in the previous example. At half-throttle,we frequently encounter ratios of 10:1 or even 14:1. A minimum of a 5:1 ratio is what I advise for acro and freestyle flying.
Though it can be more difficult to control, especially for novices, a quadcopter with a higher thrust-to-weight ratio has better acceleration and agility. To “shoot the quad into orbit like a rocket,” apply the throttle even slightly. An important part of controlling tremendous power is pilot experience and competence.
Try to achieve a thrust-to-weight ratio of at least 4:1, but preferably higher if your main intention is to fly a slow, steady aerial photography setup. More payload can be accommodated in addition to improved control.
Other Powertrain Components Are Selected Based on BLDC Motor Thrust
Propeller
The unit of thrust is grams. The propeller of your drone must generate at least one gram of thrust for every gram that it weighs in order for it to hover. Your drone need more force than one gram per gram of weight in order to carry out stunts or even just to lift off or fly forward.
When propellers spin faster, they generate more thrust; when they spin slower, they produce less. The amount of thrust generated is also influenced by the drone’s speed. Certain props work great at high speeds but not so well when hovering, while others work well when the drone is stationary but not so well during a cruise. A prop that can generate a good amount of thrust at various speeds and strikes a balance between these parameters is what you desire.
Look up motor thrust testing to determine the ideal prop size for your drone based on the size of your engine. Remember that when props are mounted to a thrust stand in a static position, they behave very differently than when they are actually flying through moving air. In the air, prop thrust might be 20–30% lower than on the ground.
ESC
The amp rating is the most crucial consideration when choosing an ESC. The maximum current an ESC can handle without breaking is indicated by the ESC amp rating. Remember that this is only a limit and not the actual current being sent to the motors, so don’t panic if it’s “too large.” An amp rating can only be too low; it can never be too high. Currently, an ESC is rated as continuous or burst. The burst current rating shows the highest current the ESC can handle for brief periods of time, usually less than 10 seconds, but the continuous amp rating indicates the steady current the ESC can safely tolerate.
The amp rating on most ESCs is more than enough for the average FPV drone pilot. The ESC amp rating is one of the most important considerations when creating a custom racing drone that needs to run at high speeds or with exceptional performance. Nonetheless, most pilots do not utilize their batteries enough to exceed the current rating of their ESCs when operating normally.
These two amp ratings are crucial since, in some circumstances, your ESC may fry or catch fire if its amp value is too low, particularly while operating at high throttle. Let’s check the thrust chart of the fpv motor of our choice and examine the Throttle and Current column.
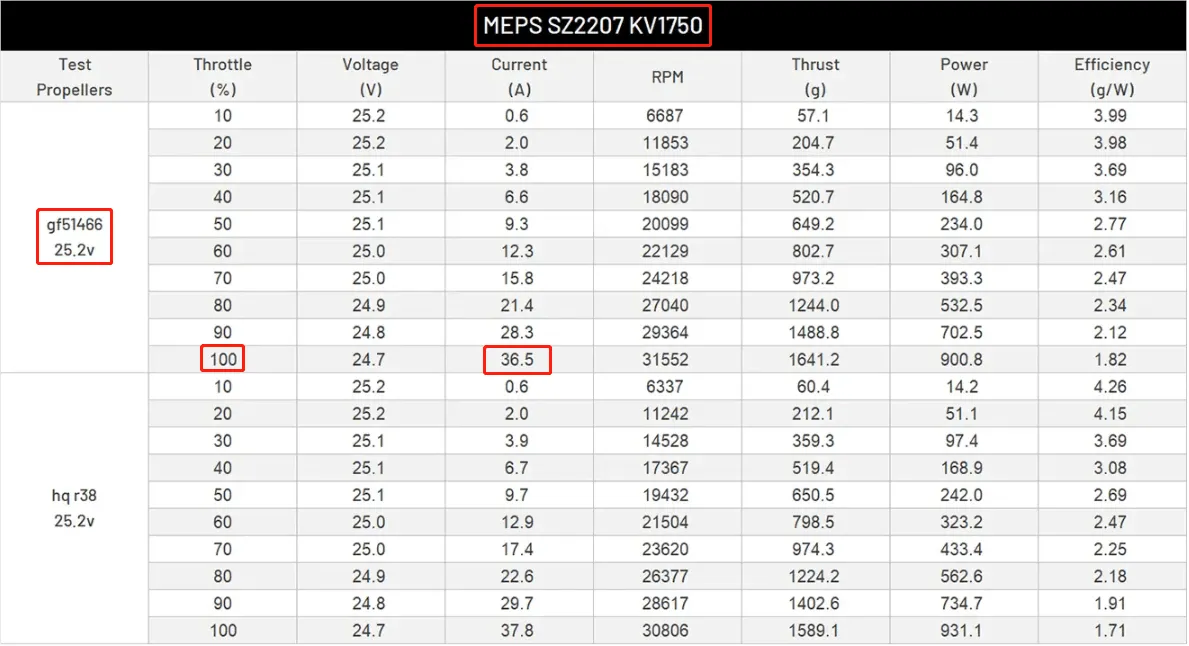
Since your burst rating can be interpreted as 100% throttle, you must select an ESC with a burst rating of at least 36.5A when using this motor/prop combination. You can use the amp draw at 80% throttle to calculate the continuous amps required for an ESC. Therefore, we would require an ESC that is rated for at least 21.4A continuous for our example motor/prop pair. Generally speaking, it’s ideal to use an ESC that is rated for a little bit more amperage than what your bldc motor and propeller combination will require both consistently and sometimes. Returning to our example, we selected an ESC with a 45A continuous and 55A burst rating for our motor/prop combination.
Battery
Since we have already selected our quad motors, we can use the thrust table of our bldc motor to ascertain the cell count lipo that was utilized.
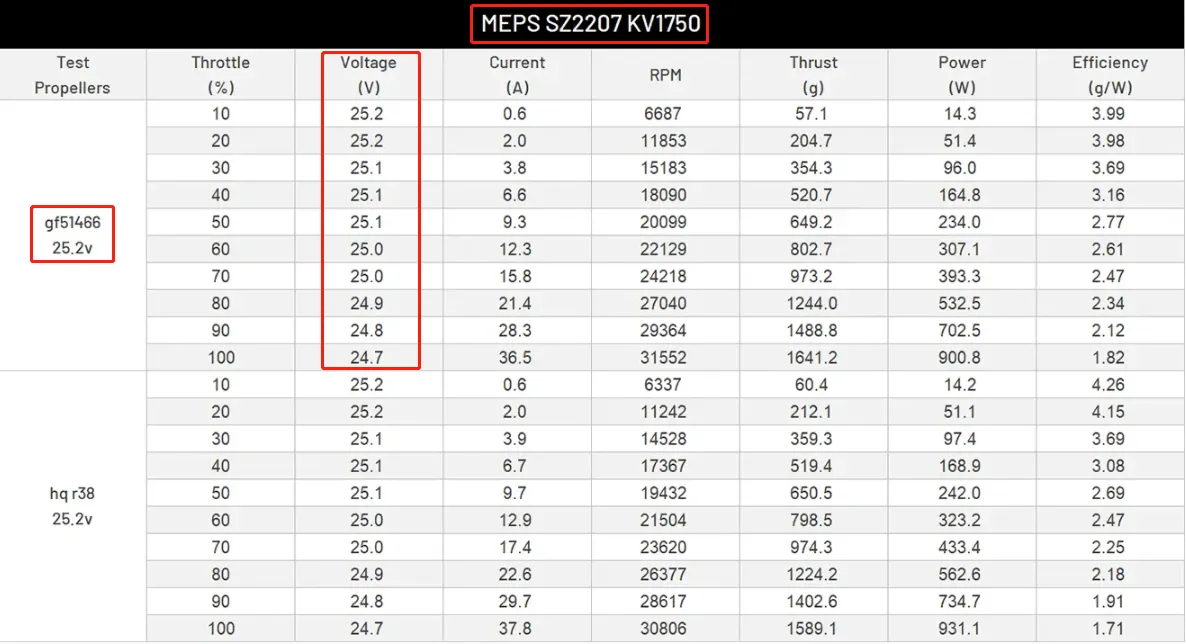
Cell Count | 1S | 2S | 3S | 4S | 5S | 6S |
Nominal Voltage | 3.7V | 7.4V | 11.1V | 14.8V | 18.5V | 22.2V |
Fully-charged Voltage | 4.2V | 8.4V | 12.6V | 16.8V | 21V | 25.2V |
Quad / Prop Size | Lipo Capacity Range |
2.5inch or smaller | 200 – 500 mAh |
3inch | 650 – 1000 mAh |
4inch | 850 – 1300 mAh |
5inch | 1000 – 1800 mAh |
6inch+ | 1500 mAh+ |
Our 1750 Kv fpv motor’s voltage column shows us that the voltage ranges from 24.7 to 25.2 V. It is reasonable to believe that 6S lipos are required for this design as a fully charged 6S lipo has a voltage of 25.2V. The larger the capacity, the heavier the battery. That’s why the capacity of the battery is not as large as it should be. Since we are building a 5 inch FPV, we chose a 1500mAh lipo. As for the discharge rate of lipo batteries, we can calculate it according to the following formula:
- Continuous C Rating = 50% of Burst C Rating = Max Current Draw / Capacity
- Continuous 60C = Burst 120C ≥(37.9V * 4 motors) / 1500mAh (1.5Ah)
We have chosen a 6S, 1500mAh, 120C lipo battery for this example fpv.
How Does MEPS Test FPV Motor Thrust?
Drone Weight Analysis
Let’s weight now, we can see, a single brick weighs 1680 grams, 5inch drone with a 4S battery weighs 530g, with a 6S battery weighs 662g, the weight is much heavier than the 4S one because we bought 1800mah 6S battery, the battery capacity is much bigger.
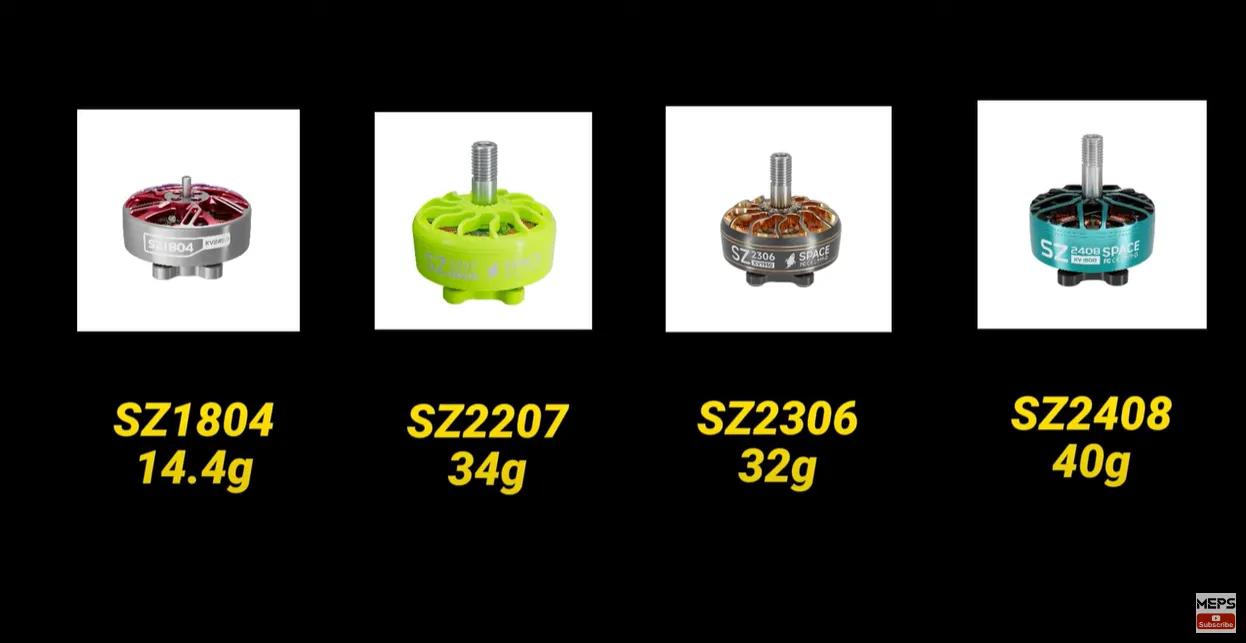
Motor Testing Process
We assume that there are currently no specifications for our motors on the website, or perhaps I don’t intend to trust the parameters provided on the official site. We will test with our own equipment, test motors of various sizes, ranging from 3 inches to 7 inches, including 1804, 2207, 2306, 2408, and 2806.5 motors. Paired with suitable propellers, we will measure their thrust, power efficiency and more.
The Test Bench of MEPS
This is the test bench we use, and it’s actually quite substantial, capable of testing large motors. We use this bench to test motors for both fixed-wing and UAV applications. Some professional pilots use much smaller testing bench specifically designed for motor testing, but for FPV drone can be sufficient.

The Testing Server
This is the testing server, you can consider it as a computer. we adjust voltage on this platform. However,it’s quite old, and some functionalities are not working that good. We are planning to replace it in the near future.
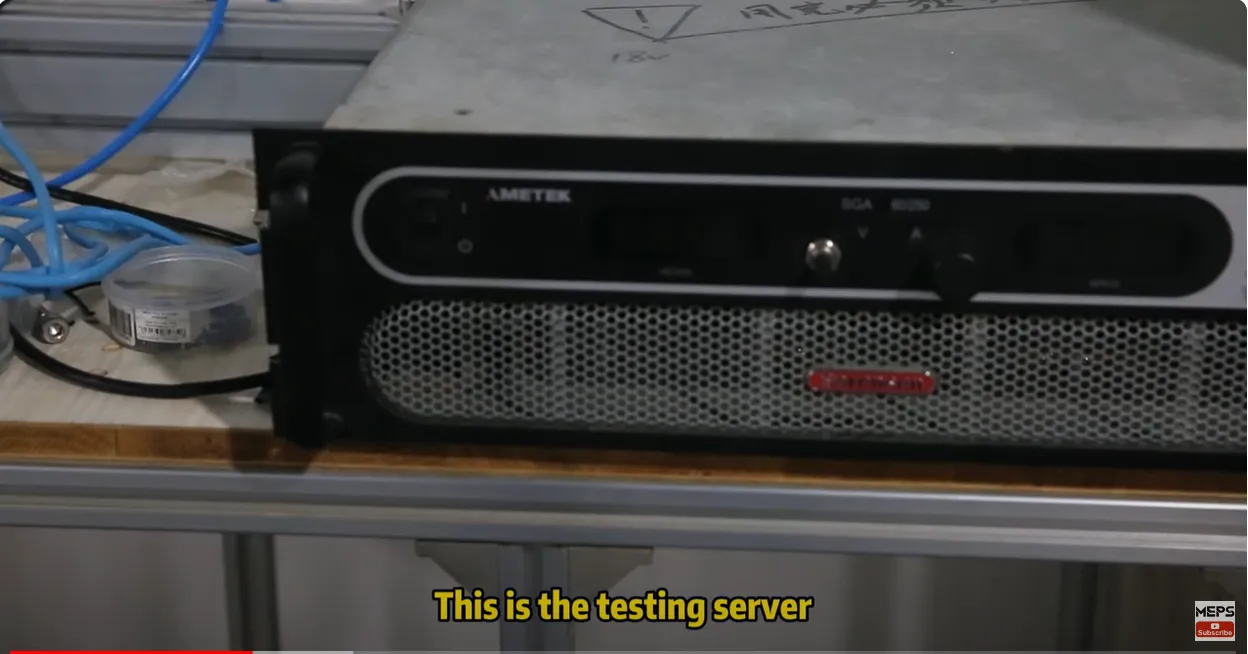
Testing Methodology
Adjust as a linear throttle, increasing by 10% throttle every 1 second until reaching full throttle at the setting voltage. After a 10-second test period, an Excel table can be generated to record various parameters.
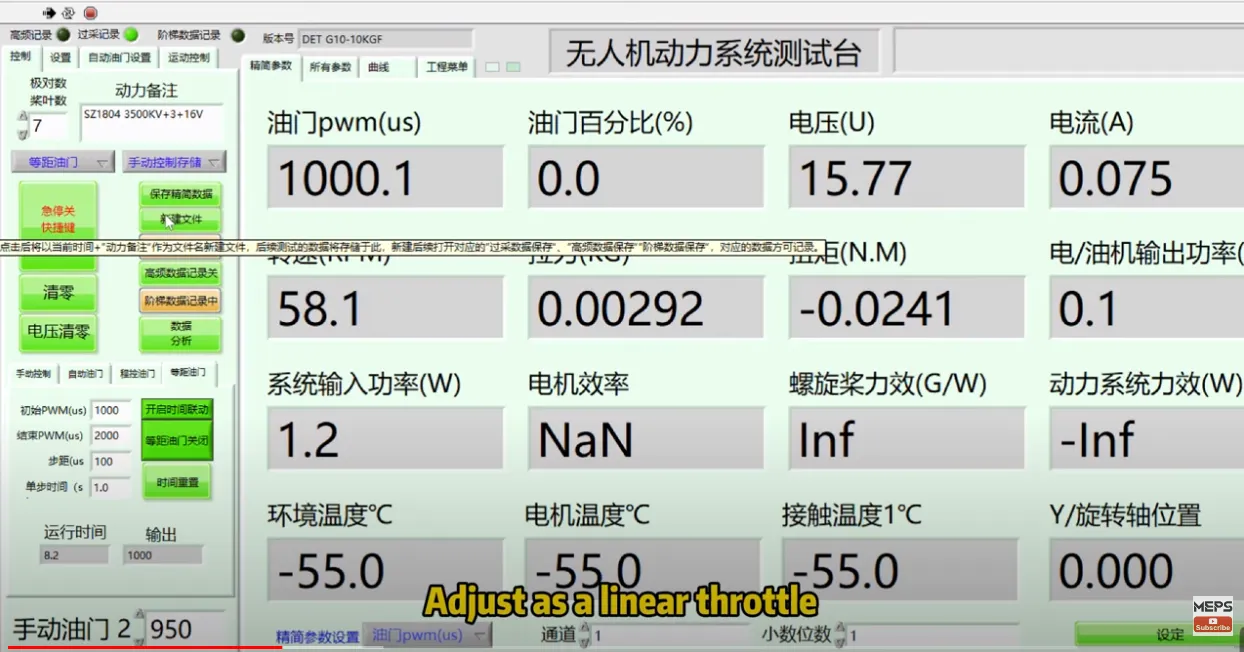
Analysis of Test Results
Now we got the parameters table here, and let’s take a look at this table, TIME represents the system time, we can ignore this, PWM is the throttle signal protocol, and then throttle, voltage, current, RPM, the F is the thrust, the T stands for Torque, Motor output power, System input power, Motor efficiency, Propeller force efficiency, System force efficiency. That’s all the parameters in the table.
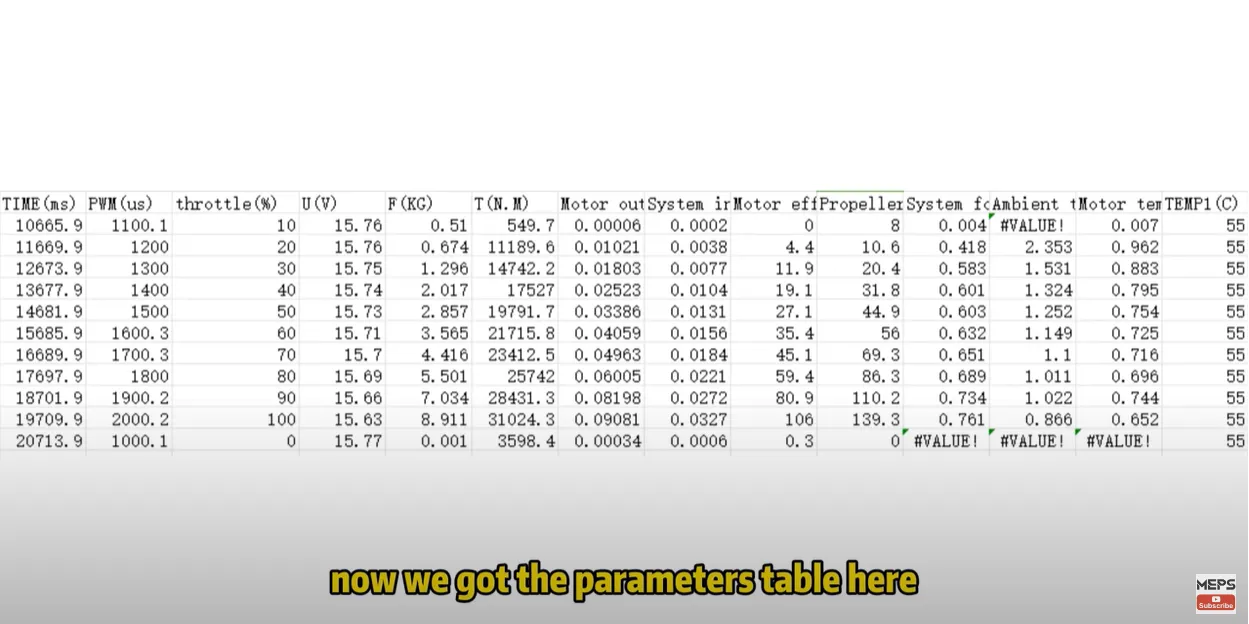
The Thrust of MEPS 1804 Motor
Now we got the 1804 motor parameters table, and we can check in the table, under 100% throttle, the thrust less than 500g, the combined thrust of the four motors is 2000g. Deducting the weight of the drone and battery, along with additional losses due to efficiency, a 3-inch propeller is unable to lift 1680g brick.
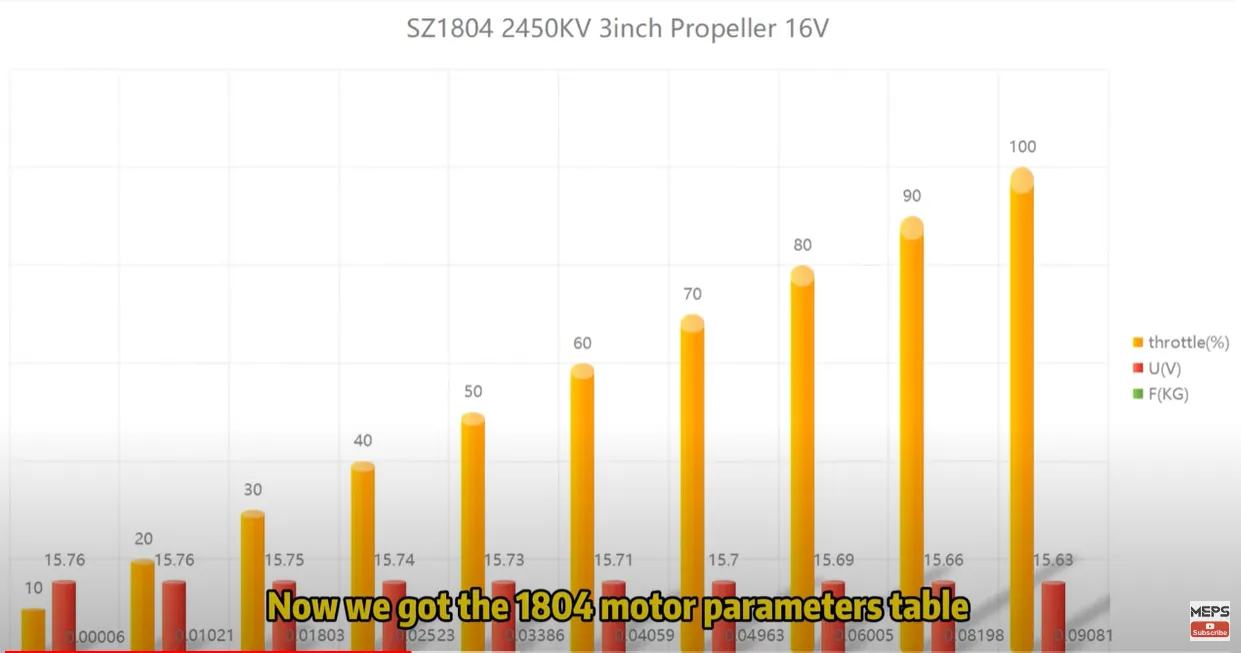
The Thrust of MEPS 2207 Motor
Our tests reveal the 2207 1950 KV motor, operating at 16 volts, is capable of generating over 1 kg of thrust per motor. Theoretically, a quadcopter equipped with these motors could support a payload of up to 4 kg. Taking into account the drone’s own weight and battery, which amounts to roughly 2.2 kg, it’s clear that the drone has ample power to ascend with ease, despite efficiency losses. In real-world tests, the 5 inch FPV drone took off successfully with a fully charged battery, though it required a bit more effort.
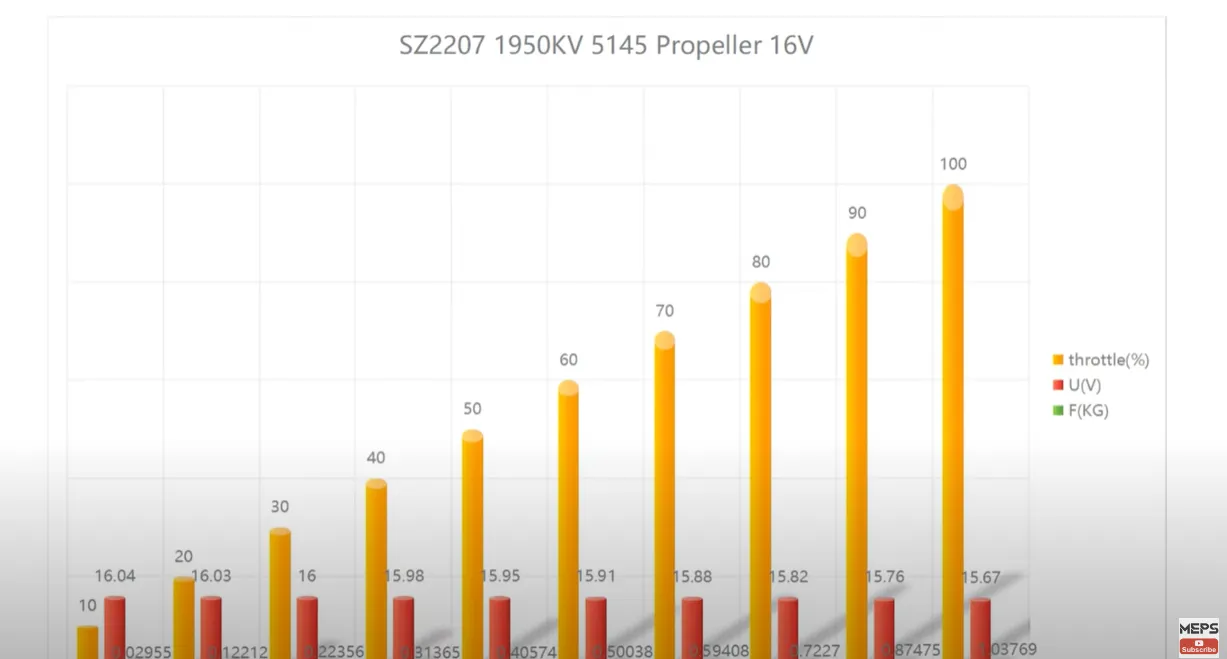
When we compared 2207 motors in 1750 KV, 1950 KV, and 2750 KV configurations, the trade-off between efficiency and power became apparent. High KV motors are ideal for racing, prioritizing power, whereas low KV motors shine in efficiency, making them suited for longer flights. Our tests, performed at 16 and 24 volts to simulate 4S and 6S battery configurations, underscore the importance of choosing the right KV rating for your flying style.

The Thrust of MEPS 2306 Motor
The 2306 1950 KV motor has a lower thrust output at 100% throttle, with only 0.85 kg per motor and 3.4 kg in total. But it shows how different motor types can be used in different ways. A higher KV motor might be better for racing, but for those looking for efficiency, the 1750 KV motor is the most efficient of all the tested motors.
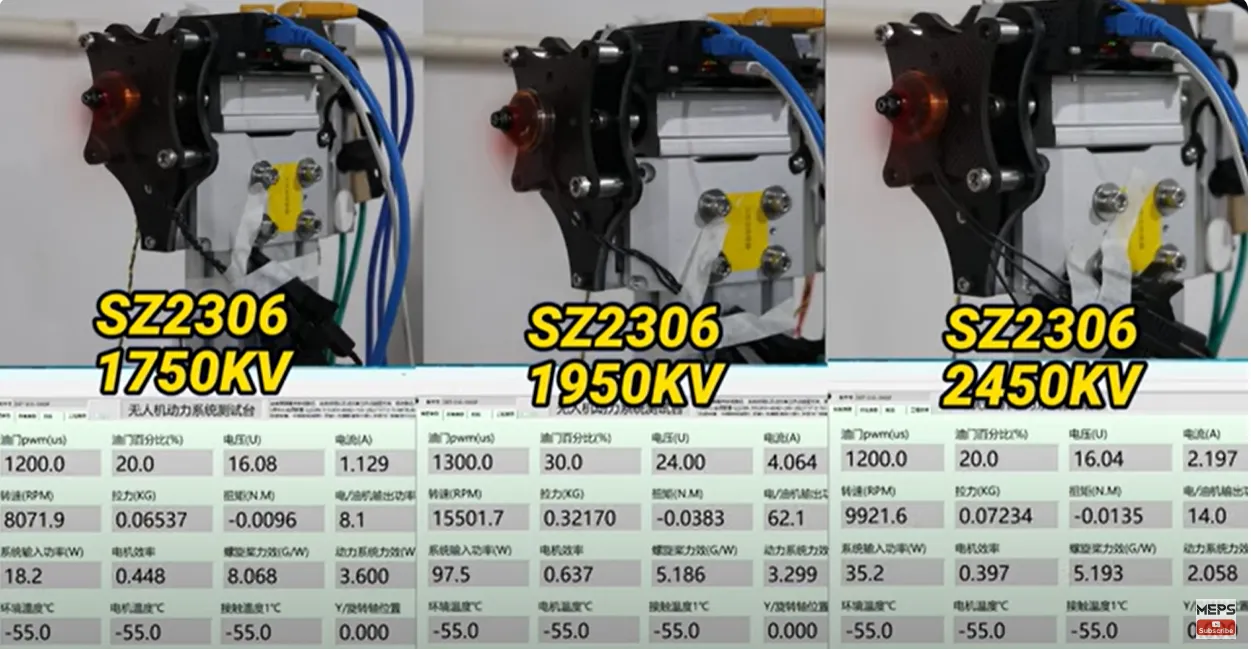
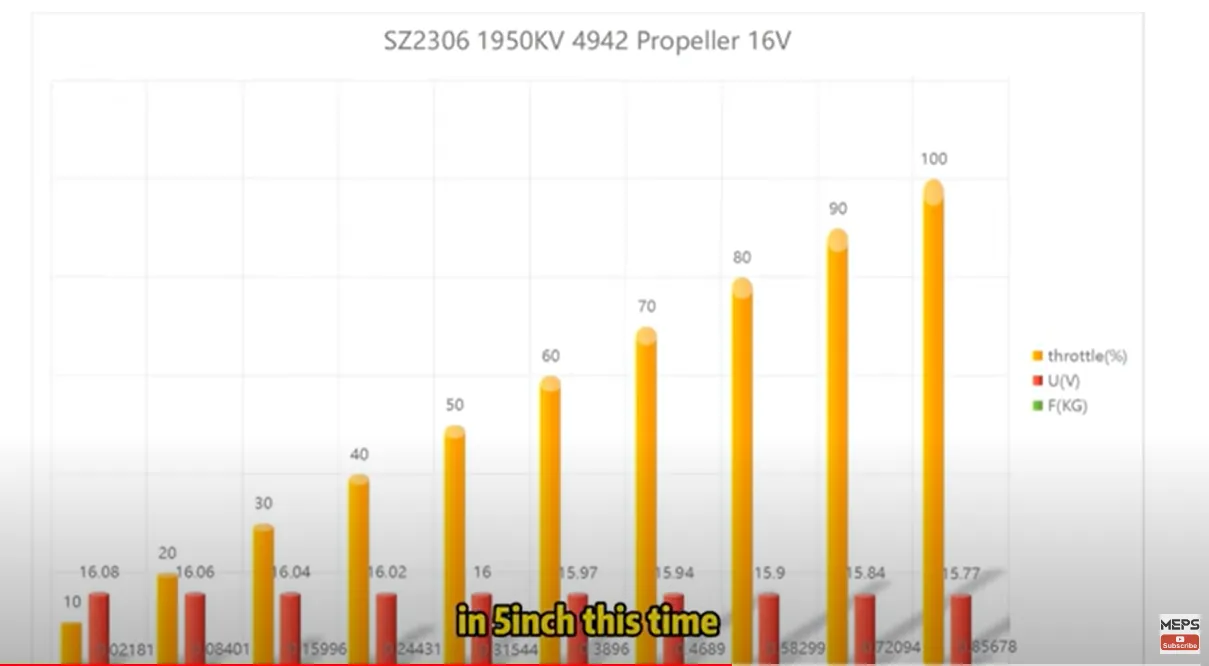
The Thrust of MEPS 2408 Motor
Our analysis extends to the 6 inch motor category, where the 2408 2500 KV motor was tested. With a 6 inch propeller, it displayed nearly 2 kg of thrust at full throttle on 16 volts, more than sufficient to carry additional payload effortlessly.
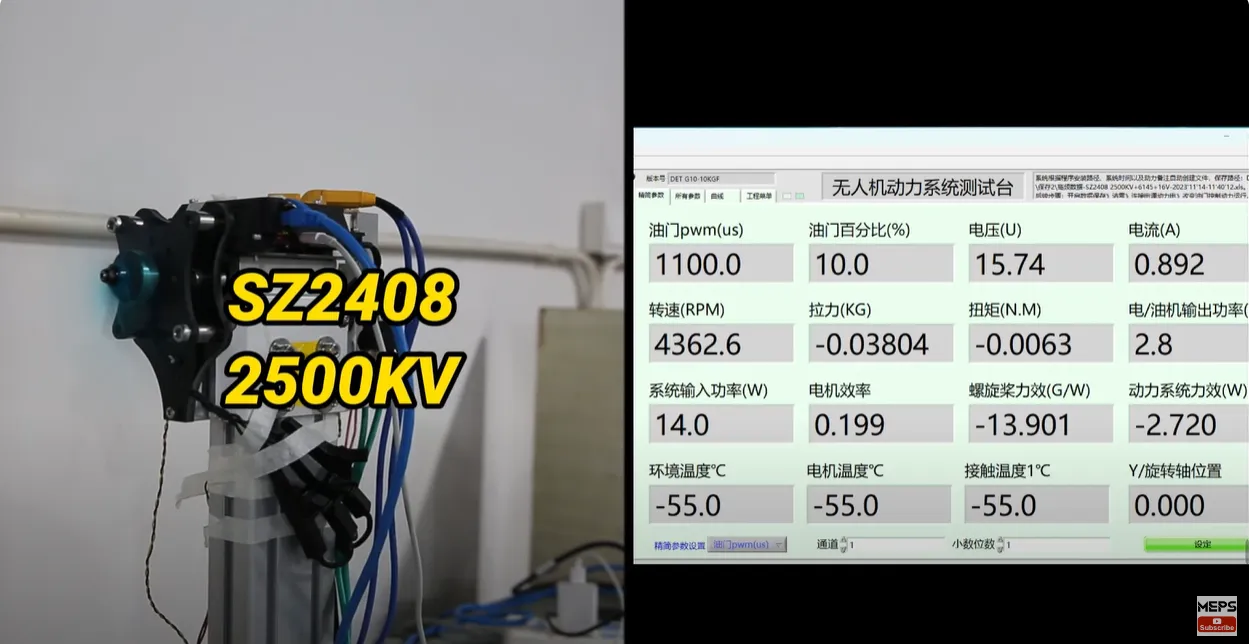
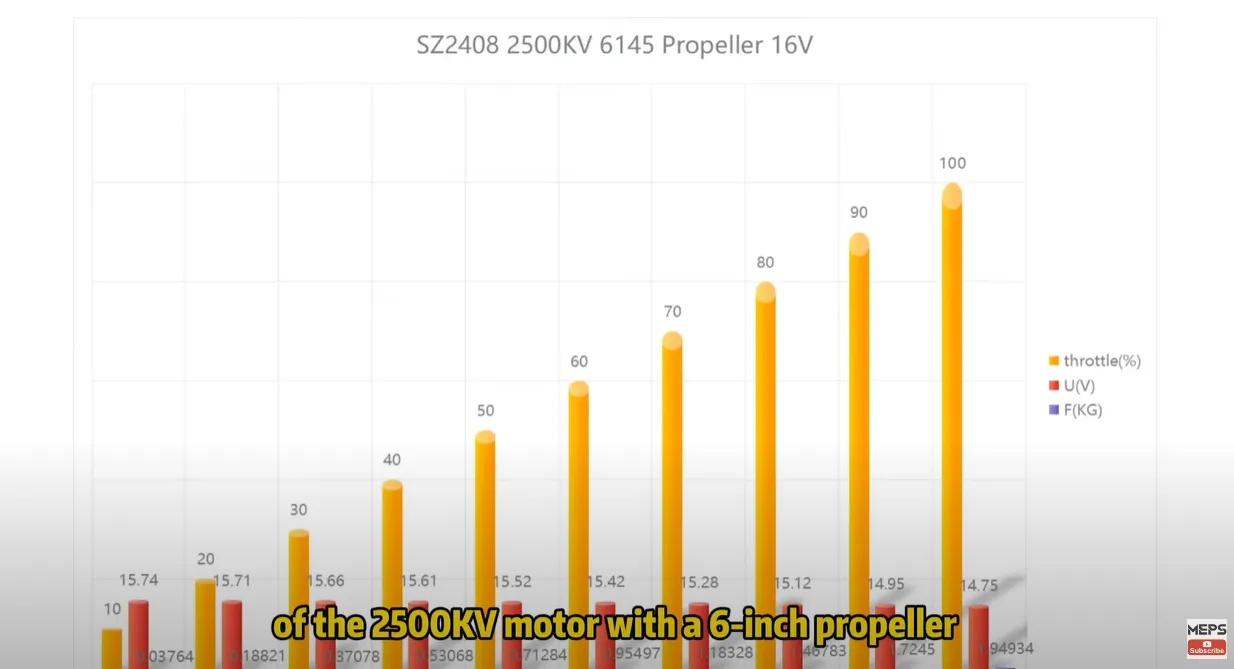
Understanding the Motor Specification Table
The SZ 2207 1750kv motor’s detailed specification table shows how it works with different propellers, at different voltages and throttle settings. It shows how throttle, current and RPM affect the motor’s pulling force and power consumption. The propeller you choose affects the thrust. The GF 51466 is better than the HQR38 at 60% throttle and above.
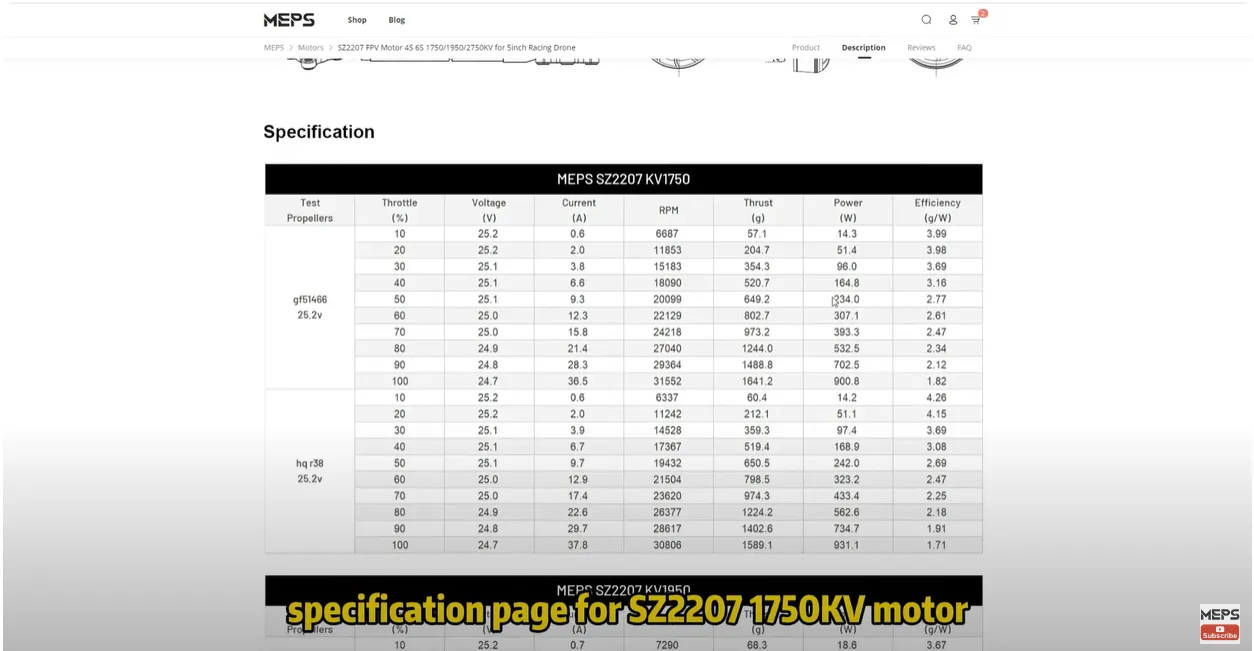
Empowering Your FPV Drone Choice
The SZ series motors are efficient and suitable for a range of FPV drones and pilots. Our motors are suitable for all sizes of frame, from 65mm to 7 inches. Our motor testing helps you choose the right motor for your FPV drone. It balances efficiency and power for the best flying experience. Whether you’re a beginner or an expert, understanding motor dynamics will improve your drone’s performance.