What is FPV motor? It is belong to uav motor. The most common use of uav motor is to spin the propellers of multirotor drones to enable them to fly.The multicopter’s flying characteristics are greatly impacted by the choice of electric FPV drone motor. Small differences in a motor’s design have a big influence on the multicopter’s weight, responsiveness, and overall power. Let’s start here to learn more about fpv motor.
When choosing fpv best drone motors , you must know the total weight of the helicopter. The calculation of the approximate weight of the drone is done by considering all the components of the drone.
First, you need to answer a few questions:
- What is the total weight of the quadcopter you plan to have?
- What are the overall structural dimensions of your fpv drone?
As for the total weight of the fpv drone, you can only assume it at the initial stage because you haven’t developed it yet. The total weight of course includes the frame, flght controller, PDB, cables, motors, ESC, batteries, payload (HD camera, gimbal, etc.) and other components. Keep in mind that the total weight at the beginning is always a conservative approximation. You can always go back and update your total weight when you finally decide on the final components you want to use in your quadcopter.
The maximum size of the frame will help you determine the best propeller size. These two important pieces of information will provide you with sufficient information about the motor thrust required to lift your quadcopter into the air using a limited size propeller.
The first place to start is with the fpv frame. If you know the size of the frame, then you can determine the right size propeller for your fpv.
Based on the weight and size of the propeller, we can determine the exact lift and flight speed of the drone. Now, we will discuss the important motor parameters that determine motor selection.
What is bldc Motor?
An FPV drone motor that is brushless has no brushes, as the name suggests. The rotor and the stator are the two distinct parts that make up a brushless motor. The core component that the rotor is attached into is called the stator. The stator is composed of a network of radial electromagnets that, when a current flows through the windings, alternately turn on and off to create a momentary magnetic field. A set of permanent magnets housed in the rotor are positioned near the electromagnets of the semi-permanent stator. Rotation is produced by the stator and rotor magnets’ attractive and repulsive interactions. After the rotor is constructed, its shaft is placed into two ball bearings in the stator to keep the rotor rotating smoothly and linearly.
The brushless motor cannot be driven directly, even though it is powered by DC current. Rather than requiring brushes or a commutator, the brushless motor is directly connected to the control electronics. Because the rotor and stator do not come into direct touch, brushless motor longevity is exceptional. In terms of efficiency, the brushless motor outperforms the brushed motor as well. In applications requiring high power outputs and efficiency—such as tiny and micro multicopter applications—brushless motors are widely used. If you want to learn more about the differences between brushed and brushless motors, check out the guide Brushed vs Brushless Motor: What’s the Difference?
Thrust-to-weight ratio
In all types of multirotors, it is important to make sure that the motors used in the drone are capable of generating about 50% more thrust than the actual weight of the drone. If all motors have less thrust, the drone will not respond well to your controls and takeoff. Even in light wind conditions, the drone motors must remain stable and function well. With a higher thrust-to-weight ratio, the drone will have greater agility and acceleration, but it will also be more difficult to control.
For example, if your drone has a total weight of 1 kg, the motors should produce a total thrust of 2 kg at 100% throttle or 500 g per motor (for quadcopters). It is always good to have more thrust than required ……
For a competition drone, the thrust-to-weight ratio is much higher than for a normal multi-rotor. For competition drones, the recommended thrust-to-weight ratio is 5:1.
If you intend to keep the drone slow and steady for aerial photography, you should keep the thrust-to-weight ratio at 3:1 or 4:1.
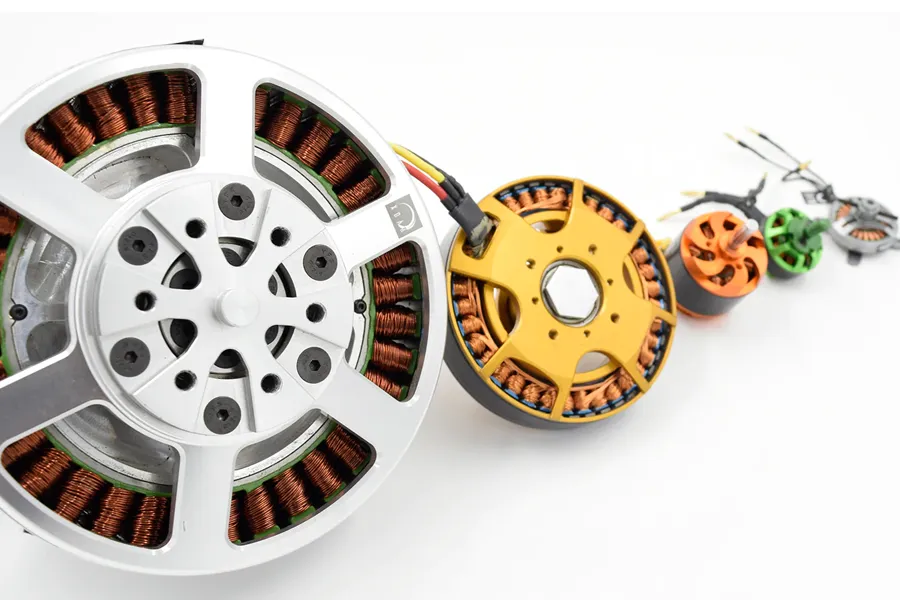
What is kv on Brushless Motors?
For example, if you choose a 1000KV motor and use a 12V lithium battery to power it, the total speed will be 1000*12=12000
After mounting the propeller to the motor, the speed will be reduced due to air resistance. a higher KV motor makes the propeller spin faster and can draw more current. This is why we tend to see larger propellers used with lower KV motors, while smaller and lighter propellers are better suited for higher KV motors.
If we pair a larger propeller with a high KV motor, more torque is needed to spin faster. While generating the required torque, it draws more current and generates too much heat. This overheating can also damage your motor.

FPV Drone Motor size
Usually, brushless motors are classified by four digits. For example, for a motor with the name 2205, the first 2 digits represent the stator diameter (in mm). The last 2 digits represent the stator height (in mm). Essentially, the wider and taller the motor is, the more torque it can produce.
- – Taller stator = more power at higher speeds
- – Wider stator = more torque at lower RPM
Since higher stators have more surface area, they can pass through more magnetic fields and help dissipate heat. And wider stators have more volume of iron and copper in the motor stator, which results in more torque and higher efficiency.
The size of motor we should use depends on the actual chassis size. This dependency is like frame size limiting propeller size and propeller size limiting motor size and KV. the table below gives you some ideas about motor size. Here, the frame size refers to the wheelbase, which is the motor-to-motor distance.
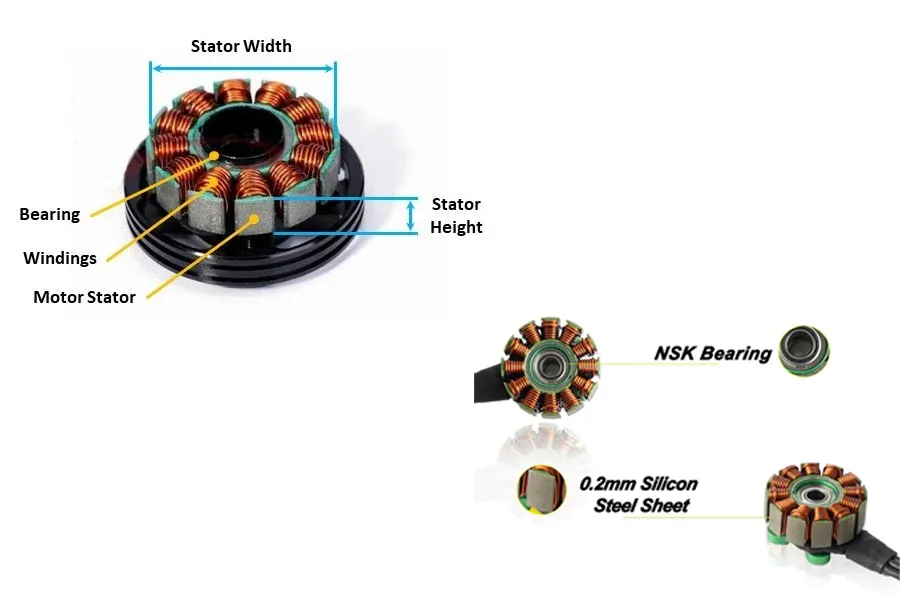
Frame size => Propeller size => Motor size and KV
In most cases, just knowing the quadcopter frame size allows us to determine the right type of motor for our project. This is because a smaller frame size means a smaller propeller size and therefore a smaller motor and a lower KV value. That said, we recommend that you review the motor thrust data to ensure that the current draw does not exceed the safe motor rating when installing the required propeller for your quadcopter.
The following table is intended to give you a simple idea and is based on the assumption that you are using a 4S lithium battery. There are many people who will use motors with higher or lower KV motors than those provided in this table. The frame size is the axis distance, which is the diagonal distance between the motors.
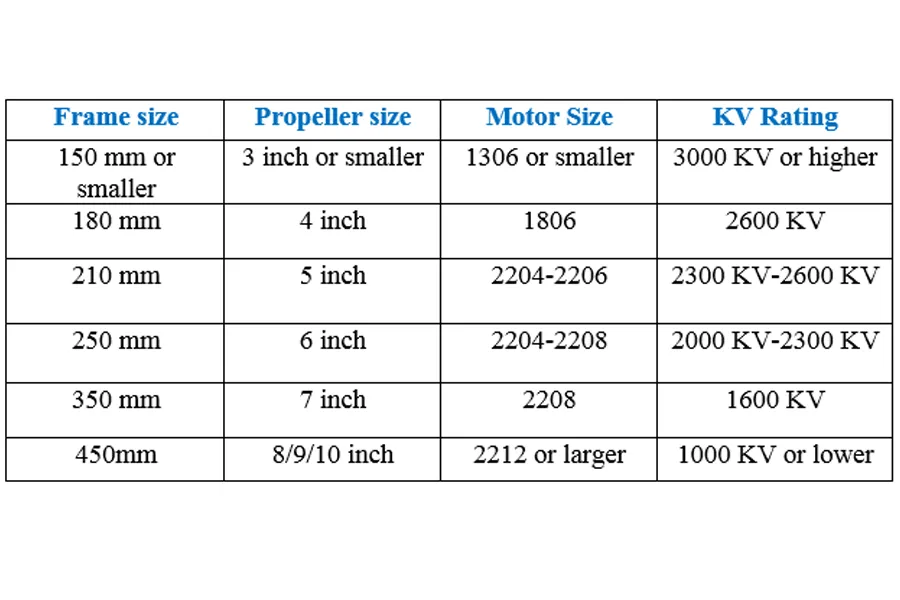
What are N and P in a Motor bldc?
Basically, N and P are the poles and magnets. If you check a motor bldc, it comes in sizes such as 12N14P. The number in front of N is the number of electromagnets in the sub and the number in front of P is the number of permanent magnets in the clockwork.
Voltage and current consumption
The voltage of the battery has a great impact on the motor bldc. The higher the voltage, the faster the drone motor spins and the more current it draws. You need to make sure how much thrust the motors produce and how much current they will draw. Depending on the current draw of the motor bldc and propeller combination, you can choose ESC.
Motor movement
If you install all the drone motors in the same direction, it will be difficult to fly the object because it will not respond to the direction you want. Therefore, to get smoother flight characteristics, you need to buy a pair of motors that move in clockwise and counterclockwise directions.
For example, if you plan to build a quadcopter, then you must install 2 motors in clockwise direction and another 2 in counterclockwise direction.
Comparison between motors
Once you have finalized the motor size and KV values, you still have many options to choose from. Here are a few things to consider when choosing the motor bldc that best fits your goals.
- Thrust
- Current consumption
- Efficiency
- Weight – rotational inertia
The final decision depends on your own preferences; it basically depends on how you want your quadcopter to perform. By injecting more thrust, you can achieve faster speeds. At the same time, you need to make sure that the device is efficient enough; that is, that it does not consume more power than the hardware in which it is mounted can support.
Also, keep in mind that your preference for motors and propellers may affect the batteries you use. If your motor is capable of drawing optimal current from the battery at 100% throttle, it must be equipped to support a discharge rate based on the power required. In addition, you need to ensure that the battery does not overheat and discharge too quickly. You can check the C rating for this.
Another aspect that most drones are not too concerned about is motor bldc weight. For competition drones, this is an important factor. In addition to affecting the total weight and weight-thrust ratio of the quadcopter, it also affects the rotational inertia of the device. For example, when performing aerial stunts such as rolls and flips, your quadcopter will need some time to gain the necessary angular acceleration and fly down to the target point. With heavier motors, the quadcopter may take more time to complete this maneuver, thus giving you the impression that it is not as responsive as you would like it to be.
In fact, the whole game is about bringing much needed balance or an area where you want your quadcopter to perform better at the expense of another!

More tips on fpv drone motor efficiency
The lighter the multi-rotor RC plane, the more efficient the performance. This article explains how to strike the ideal balance between choosing a lithium polymer battery for your multi-rotor device. When it comes to overall power efficiency, batteries and weight are not the only parameters that have a say in this complex equation.
When choosing the right motor, we need to consider motor efficiency in addition to motor KV and thrust. This is more or less similar to riding a bicycle. When riding a bicycle, you can move faster when you are in a lower gear, but you also have to pedal faster while facing greater resistance. When climbing increasingly steep and rocky terrain, pedaling becomes more difficult as time passes. There will always be a point in time when, despite how hard you pedal, your speed will get slower and slower. This is the point at which you will lose efficiency.
The same process applies to brushless motors. The higher the efficiency, the better it is for your quadcopter. A motor with 70% efficiency means it will produce 70% of the electricity and consume 30% of the energy in the form of heat. On the other hand, a 90% efficient motor will produce 90% of the power and only 10% of the energy will be lost in the form of heat.
If you use a less efficient motor, this will result in more heat loss and thus shorter flight times. In addition, you will not get enough thrust at full throttle. More importantly, you will not get the necessary response from the device due to the inefficient motor. The motor will reach its target revolutions per minute over a longer time interval, which will negatively affect stability and responsiveness.
We hope this blog has helped you understand the parameters of quadcopter motors.
Here are the videos about the motor: